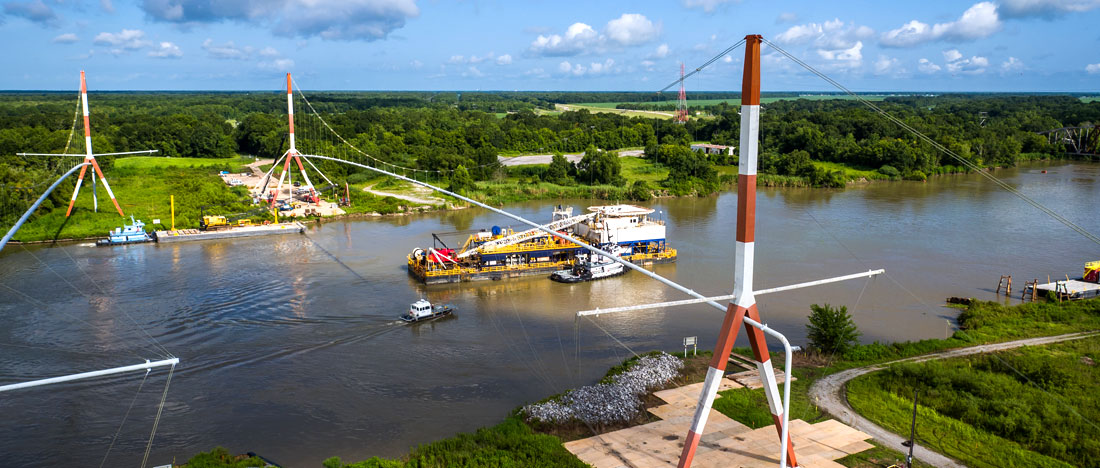
Aerial Pipeline Abandonment Reaches New Heights
What goes up must come down.
The world has changed quite a bit since the 1970s, and the oil and gas industry is no exception. Improvements in safety, training and technology have changed the way we approach complex projects for the better. At MORRISON, we recently found ourselves faced with a challenge that had no obvious precedent: how to safely remove and dismantle a 22” aerial pipeline over fast-moving water.
This particular pipeline, like many others across the country, was originally installed in the 1970s. Back then, the only option was putting workers in boxes up to 80 feet in the air. But now, that level of risk is less tolerable, and ideally it is avoidable, given the right combination of creativity and expertise. In the end, we proved this kind of work could be performed safely and efficiently by completing the first ever aerial pipeline abandonment and dismantlement in the country.
The key to success with a project of this nature is planning. Working closely with the owner, Shell Pipeline, our team developed a work scope that was both efficient and met stringent regulatory and safety requirements.
With no other examples of this kind of work to reference, we had to start from scratch.
The pipeline in question spanned more than 800 feet between inverted-Y towers on the banks of Wax Lake Outlet, located in the Atchafalaya Bay in South Louisiana. Suspended from cables 73 feet above sea level, bringing down the pipeline, cables and towers would be no easy feat. The biggest risk would come from putting workers at height to perform the necessary cuts, but there was also concern about the fast-moving water between the two shores, where boat traffic was frequent. The site itself on either bank was also problematic, with nearby levees making it difficult to bring in the normal array of large equipment used for a project of this size. And finally, we had to account for the expected challenges (unsprung energy storage, environmental concerns) as well as the unexpected (inclement weather and lightning).
We developed a plan that successfully managed all of these challenges, and worked closely with the team from Shell Pipeline to ensure that every step of the process was managed safely. In order to make the job site more stable, we started by installing interlocking mats on both banks to provide the necessary support and traction for vehicles and workers. A fit-for-purpose equipment spread included several of our barges capable of supporting a crane and transporting 50-foot pipe segments after removal.
Solving the challenge of cutting at heights while mitigating risk was a top priority, so we identified a unique solution that avoided the problem altogether.
Part of our initial approach was to contact the original designer of the aerials to find out how they were installed. Doing this gave us insight that allowed us to reverse-engineer the project, tweaking it as needed to make it safer and more efficient. With the cables safely cut and the pipe ends excavated, nitrogen was pumped into the pipeline to de-water it. Then, one at a time, the towers were lowered to a 45 degree angle, dropping the pipeline end onto the deck of the barge where it was cut into segments. By slowly raising or lowering the tower, the crew was able to perform all the necessary cutting on the barge deck.
Complicating the operation somewhat was the routine recreational boat traffic through the site, which happened to be near a public boat launch and Highway 90. In order to avoid disrupting local activities too much, we worked with the local sheriff’s department to help manage the waterway. The combination of law enforcement boats and lights was effective at cautioning vessels in the area, and through close coordination with the work crew, boats were escorted safely through to the other side. This creative approach served both the project’s goals and the local community, who would have been negatively impacted by any closures to the waterway.
Lessons learned
Ultimately, the success of the project – which was completed on schedule and incident-free – was due in large part to our close partnership with Shell. Both in the planning stages and during the dismantlement, our teams worked in careful coordination to make sure we were prepared for anything. Project managers were on-site throughout the duration of the work to supervise and manage any changes that might be needed.
In this case, it was our collective experience and expertise that drove the solution. Taking what they knew from other pipeline abandonment work and adding in the necessary engineering know-how, we planned a meticulously organized operation that accounted for every possibility and mitigated risk at every step.
“This project really illustrates how working with us early in the planning stages can pay dividends. In this case, our early involvement led to better safety, efficiency and ultimately a successful result.”